فيبر جلاس
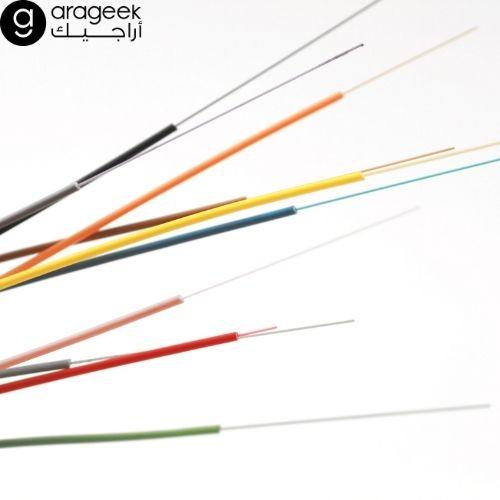
تم التدقيق بواسطة: فريق أراجيك
يمكن تقسيم المواد الزجاجية إلى ثلاثة أجيال: الجيل الأول، الأقدم والأكثر متانة والأكبر سناً، هو جيل زجاج البورسليكات (تُصنع منه أدوات المطبخ الزجاجية) وزجاج الصودا والجير، المتعارف عليه في صنع البرطمانات الزجاجية والنوافذ. أما الجيل الأخير، أو لنقل الجيل الفتيّ المشهور كثيراً، هو جيل كابلات الألياف الضوئية، التي تُستخدم لنقل جميع اتصالاتنا تقريبًا اليوم، صغيرٌ ولكنه يجذب الانتباه كثيراً ويُدرّس. أما الجيل الأوسط الثاني، فيُعتبر مظلومٌ مجتمعياً، هو على نفس القدر من فعالية الجيلين سابقي الذكر، ولكنه يعمل "خلف الكواليس"، بحسب تعبير جون سي ماورو؛ باحثٌ وعالم مواد متخصص في الزجاج في جامعة ولاية بنسلفانيا، إنه الفيبر جلاس، أو كما يدعوه البعض "الفايبر جلاس"، أو كما هو متعارف عليه أكثر "الليف الزجاجي".
تعريف الفيبر جلاس
الفيبر جلاس (Fiberglass) أو الليف الزجاجي، يُطلق هذا الاسم على المادة المُنتَجة من الأسلاك الزجاجية الرقيقة جداً المنصهرة من قوالب الزجاج، نوعٌ من البلاستيك المقوّى، تتكون من مادة مدمجة منسوجة بألياف زجاجية، يتم وضعها بشكل عشوائي عبر بعضها البعض وتثبيتها معاً باستخدام مادة ملزمة. وتُصنع الألياف الزجاجية من أنواع مختلفة من الزجاج، ويعتمد النوع المُختار على الغاية من الليف الزجاجي. أما عن أشكالها، فيُمكن أن تُسطّح على شكل صفيحة، أو أن تُرتّب عشوائيًا، أو تُنسج في قطعة قماشية.
يُستخدم الفيبر جلاس في العديد من الصناعات، مثل بناء المنازل والأسقف المسطحة؛ أي يُستخدم الليف كعازل، لذا غالبًا لا يلاحظه أحد لأنه يكون مُغطّى أو مخفي، كما يُستخدم في تصنيع القوارب، ويمكنك العثور على الفيبر جلاس في هياكل مركبات النقل، وفي العديد من معدات التّصنيع. هي مركبات قوية وصلبة وخفيفة الوزن، وهذا هو السبب في أن شركات صناعة السيارات والشركات المصنعة الأخرى، تستخدم هذه المواد المعززة لبناء منتجات موفرة للوقود والطاقة، ويُعتبر الفيبر جلاس قليل التكلفة بالمقارنة مع غيره من المواد ذاتُ نفسِ التأثير.
تطور صناعة الفيبر جلاس
ربما بدأ الأمر من الفينيقيين والإغريق وقدماء المصريين، حيث فهم هؤلاء كيفية صنع خيوط الزجاج الدقيقة، واستخدموها لأغراض الديكور، ولكن مع تقدم الزمن، فهمت الشعوب أن إنتاج بعض الخيوط اليدوية من الزجاج، يختلف بشكلٍ كبير عن إنتاج عدد كبير من الألياف، ولذلك بدأ الناس في الأماكن المختلفة بتجربة تقنيات جديدة في القرن التاسع عشر.
عام 1880، قُدمت أول براءة اختراع لإنتاج الألياف الزجاجية في الولايات المتحدة، لرجلٍ يُدعى هيرمان هاميسفهر (Hermann Hammesfahr)، حيث طوّر نوعًا من القماش المنسوج من الألياف الزجاجية والحرير.
عام 1932، حدثت الكثير من التطورات، فنتيجةً للركود الاقتصادي الذي خفّض الطلب على القوارير في مدينة توليدو في أوهايو، شعر صانعٌ للزجاج بالاكتئاب، وطلب من المهندس الذي يعمل لديه، جيمس ستيلر (Games Slayter)، بالعمل على إيجاد طرق لإنتاج الألياف الزجاجية كاستراتيجية لإيجاد أسواق جديدة للزجاج. كما كان يعمل رجل آخر في منطقة أخرى على دمج كتل الزجاج معًا، ورشّها كخيوط زجاجية باستخدام مسدس مصمم أصلاً لرش البرونز المصهور.
خرج ستيلر بأول منتج تم تصنيعه باستخدام الألياف الزجاجية الجديدة، وهو عبارة عن مرشح هواء طُرح في الأسواق في عام 1932. وكان هذا أول منتجٍ ناجحٍ تجاريًا، مصنوع من الألياف الزجاجية.
طريقة تصنيع الفيبر جلاس
Time needed: 11 days, 11 hours and 5 minutes.
تمرّ عملية صنع الفيبر جلاس بـ 5 مراحل أساسية، هي:
- مرحلة الخلط
طبعًا تتكون الألياف الزجاجية بشكل رئيس من السيليكا، ويمكن صنعها تجاريًا من السيليكا فقط، ولكن غالبًا ما تتم إضافة وخلط مكونات أخرى تُنتج خصائص معينة للفيبر، كما تعمل هذه المواد على تخفيض حرارة العمل. أهم المواد المُضافة في هذه العملية: أكسيد الألومنيوم، وأكسيد الكالسيوم، وأكسيد المغنزيوم، وكربونات الصوديوم، والحجر الجيري والطين وأكاسيد أخرى كثيرة، كل منها يساهم في صنع نوع معين من الزجاج.
- مرحلة الصَّهر
يُنقل الخليط إلى فرن يعمل بالغاز الطبيعي، مع درجة حرارة عالية، حوالي 1400 درجة مئوية، ويجب أن يتخطى 3 مراحل في الفرن: المرحلة الأولى في القسم الأول من الفرن، يتم الصّهر، ثم في القسم الثاني، تتم تصفية الخليط المصهور، وتكون درجة الحرارة هنا 1370 سيليسيوس. أما في المرحلة الثالثة، يتدفق الزجاج المصهور إلى بطانات مصنوعة من البلاتين والروديوم، والتي تعمل على قذف الزجاج المصهور وتحويله إلى ألياف.
- مرحلة تكوين الألياف الزجاجية
يتم تكوين الألياف بفضل عمليتي البثق والتوهين. يمر الزجاج المنصهر خارج المدخنة، من خلال جلبة مصنوعة من سبيكة بلاتينية أو من الروديوم، مقاومة للتآكل، مع فتحات دقيقة جدًا في الجلبة؛ إذ قد تحتوي الجلبة الواحدة على 200-8000 فتحة. والآن، تُسخّن ألواح البطانة إلكترونيًّا، ويجب معايرة درجة حرارتها بشكل يسمح بالحفاظ على لزوجة زجاجيّة ثابتة. فور خروج خيوط الزجاج من الجلبة، تعمل نفاثات الماء، من أجل التبريد. وأخيرًا، يتم سحب خيوط الزجاج باستخدام جهاز لفّ عالي السرعة؛ حيث يدور بسرعة أكبر من سرعة خروج الزجاج المصهور من البطانات، وبتأثير قوة الشّد، تنتج خيوط رفيعة بقطر 4-34 ميكرومتر (ما يعادل 1/10 من سماكة شعر الإنسان).
- عملية التغطية أو التكسية
تسحب اللفافات الميكانيكية الألياف الناتجة بسرعة خطية تبلغ 61 m/s، وذلك من خلال قضيب يقوم بتغليف الألياف بطبقة كيميائية، وتُعتبر هذه العملية معالجة إضافية لتحسين جودة المُنتَج النّهائي.
- المرحلة النهائية: التجفيف والتغليف
وهنا تُجمع الخيوط المسحوبة ذات الحجم الموحد معاً في حزمة، بحيث تشكل الحِزم في مجموعها 51 إلى 1624 خيط. تُدرج هذه الخيوط وتُلف على أسطوانة في أداة تشكيل تشبه في شكلها بكرة الخيوط، ثم تُجفَّف عبوات التشكيل في الفرن، ثم تُصبح جاهزة وتُنقل إلى منصات ليتم إما شحنها أو معالجتها إضافيًّا لتتحول إما إلى ألياف مقطعة، أو روفينج؛ حزمة طويلة وضيقة من الألياف، أو غير ذلك.
في النتيجة: يبقى من الهام بالنسبة للكثيرين ممن يستخدمون الزجاج في حياتهم أن يعلموا الكيفية التي تمت صناعته فيها، ربما للاطمئنان أو للشعور بأن ما يستخدمونه لا يسبب لهم الضرر.
اقرأ أيضًا: ما هو الصوف الزجاجي وما هي مخاطر استخدامه؟